Horizontal Deposition Sputtering System
The SCT Axis series sputter systems were designed with flexibility in mind and have a proven track record of reliability.
All Axis sputter systems have load-locks for high throughput and come with a choice of two (Axis II), three (Axis III) and four (Axis IV) target configurations. RF magnetron, RF diode and DC magnetron cathodes are available at each cathode position. Two styles of cathodes are offered: planar and inset, the latter allowing for three distinct target shapes.
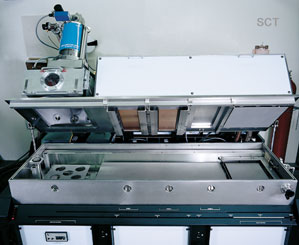
Load-Lock and Process Chambers
The Axis processes one pallet at a time, but the addition of a two-level load-lock allows for simultaneous loading and unloading of pallets while sputtering and etching takes place in the process chamber.
This horizontal sputter system has multipass scanning capability – if a particular cathode cannot deposit enough material on the substrate on one pass as called for in a particular process, the system has the capacity to reverse direction, and continue as often as needed.
The cathodes are all equipped with cross contamination shields which prevent adjacent target contamination during sputtering.
The RF etch station is standard, and contained inside the process chamber thereby reducing the substrates’ exposure to atmosphere. The etch platform is water-cooled and pneumatically actuated. It operates by lifting the pallet off the pallet carrier for etching. A shutter, placed directly above3 the pallet, acts as an etch catcher and a ground plane.
The RF generator and the DC power supply are housed under the chamber within the system’s frame. A 10kW DC power supply is standard, with an option for 20 kilowatts. For RF magnetron or diode operations, standard power is 1.5kW, with 3kW optional.
Programmable High Vacuum System Controller with Data Logging Capabilities
SCT provides as a standard a PLC control system which includes ladder logic software with required programming for the SCT Axis, written specifically to accommodate customer specifications. The operator/engineer computer interface includes a touch screen display, HMI, and all required software programming. The control system also can perform data logging of all key process variables.
As an option, SCT can customize reports of the data to meet specific customer requests.
Custom Features
All of SCT’s systems are built to customer specifications, making each system in some ways unique. Our engineering department can make any desired modifications to the basic design so that we can provide you with a fully documented custom system tailored to your specific requirements.
Here are some of the features which are available:
- Hi-vacuum load-lock with the addition of cryopump for shorter cycle times
- Substrate heat available for both load-lock and process chamber
- Load-lock cooling by adding an inert gas to the load-lock
- Two, three and four cathode configurations—any combination of planar and inset, RF or DC
- Inset style cathodes can be outfitted with three separate target material shapes—one at a time, of course
- Can be configured with up to four process gases
- RF voltage stabilization
- DC bias capability includes internal mechanism to apply DC power to the pallet. This option includes a 150V power supply.